供稿:通快(中国)有限公司
波长在 1 µm 左右的碟片激光器和光纤激光器,正日益应用于 各种不同的焊接任务中,并且正在从 CO2 激光器手中抢占到越来越多的市场份额。尤其是在薄板焊接、三维部 件焊接以及大型部件焊接等应用中,1 µm 波长通过柔性光纤导光的优势是非常有用的。但是如果关注的焦点 是焊接质量标准,比如焊缝表面和焊 缝底部的焊接质量以及焊接飞溅物,那么CO2激光器则是最常用的光源选择。
本文将着重探索深熔焊引发加工过程不稳定的机理,并通过高速成像 设备记录画面,以便探讨提高固体激光器焊接质量的解决方案。首先要解决的问题是如何在工业生产环境中优 化加工工艺,从而优化加工的可靠性。第二,如何抑制金属羽辉,从而优化应用结果和增加熔深。第三,如何使用远程扫描头焊接和摆动技术来优化应用结果。
优化应用结果的方法
(1)试验装置
采用通快的 Yb:YAG 固体碟片激光器(TruDisk 16002)对低碳钢 S235 进行局部穿透和全部穿透的深熔焊,光束质量为 8mm*mrad,波长λ= 1.03 µm。为了实现更大的穿透深度和更高的焊缝质量,焦点位置设 定在工件表面以下 2 mm 处。在焊接材料底部安装有一台高速相机,其与一台 EOS 7D 相机和安装在焊接材料 顶部的其他高速摄像机结合使用,可 以非常详细地以可视化的方式记录整个焊接过程。下面我们将主要研究三个主要现象:熔滴、飞溅物和金属羽辉。
图1:试验装置
(2)使用 1 µm 碟片激光器或光纤激光器实现全熔透焊接
对于全熔透焊接,焊接参数对焊缝质量的影响非常大。图 2 中显示了激光功率参数对焊缝质量的影响。从图中可以看到,当激光功率从 7.75 kW 增加到 13 kW 时对焊缝质量的影响。该试验是在厚度为 12 mm 的低碳钢 S235 上进行的,焊接速 度恒定为 1 m/min。当激光功率为 7.75 kW 时,我们可以看到熔池的影响。在进料的反方向上,处于熔化节点和激光束出现点之间存在一个几毫米的缺口。当激光功率 为 8 kW 时,熔池移动到了激光束出现之前,从而出现 微小熔化增多,避免了熔滴。进一步增加激光功率,会导致熔化节点和激光束出现点之间更大的差 距。当功率为 10 kW 时, 能获得1.1 mm 的最大熔深。熔池动态受到了影响,并且 在底部可以检测到一 个旋转的熔体流动。
(3)飞溅物和金属羽辉
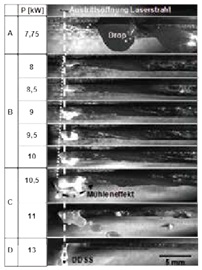
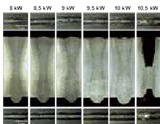
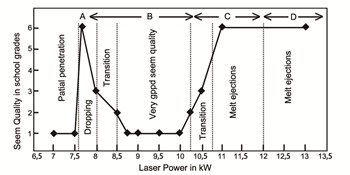
a) b) c)
图2:以1 m/min的速度对厚度为12 mm的薄板进行全熔透焊接时,激光功率对焊接质量的影响。a)在左 边可以看到焊接材料的底部,包括出射激光束的位置。b)材料上表面的焊接质量、截面和下表面的焊缝 质量。c) 焊接质量处于实验级别,这里1表示质量非常好。
由于毛细管后方的表面张力,熔体向工件偏转——一 种所谓的“研磨效应”由此产生,导致在工件底部的焊缝 强度得到加强。因此,当激光功率在 8.5~10.25 kW 之间 时,可以获得非常好的焊缝质量。在这样的功率水平下, 熔池底部没有开口的毛细管,因此在根部没有检测到飞溅 物。当激光功率达到 10.5~13 kW 时,这种现象会有所改 变,这时候熔体会在底部喷射出来。当激光功率达到 13 kW 时,熔体喷射非常厉害,导致工件分离,从而形成切割(没有任何辅助切割气体)。这种效应被称为蒸汽压力熔切(VPMC)。图 2b 中分别显示了工件顶部、底部以及截面的焊缝质量。若将焊缝质量的等级以数字区分,1 代表 质量非常好,而 6 代表质量很差。我们可以看到,对于 12mm 厚的低碳钢来说,在激光功率为 8.7~10 kW 之间时, 可以实现深熔焊并获得良好的焊接效果。在实际工业应 用中,我们建议的选择功率为 9.25 kW(即大约处于功率 中点),以便增加激光加工过程的可靠性。正如上文提及, 该试验是在进给速度为 1m/min 的情况下进行的。
除了测试不同的激光功率对焊接质量的影响外,我们 也评估了不同的进给速度对焊接质量的影响。试验所用板 材的厚度仍然为 12 mm,并且采用相同质量标准。结果如图 3 所示。
在所有的激光焊接进给速度下,我们可以看到有的区域全熔透了,但同时伴有熔滴滴落。激光功率的增加可以 使这个区域扩大,从而实现足够好的焊缝质量(见图 3,B1 和 B2 域)。由于高能量的输入,B1 区 0.2~0.7 m/min的低焊接速度,会导致更宽的焊缝。随着进给速度的增加, 焊缝随之变小,但是焊缝所处的功率范围也在缩小(图 3,B2 区域)。当焊接速度 v = 1 m/min 时,功率变化范围 ΔP 约为 2.5 kW ;当焊接速度 v = 1.5 m/min 时,功率变 化范围缩小到 ΔP = 0.25 kW。当焊接速度超过 1.5 m/min 时,就很难获得较好的焊接效果,将会产生熔滴滴落,或者出现蒸汽压力熔切。
图3:在厚度为12 mm的低碳钢S235材料上的应用结果。 图4:不同进给速度下的侧面图。
当焊接速度为 v = 3~4 m/min 的中等速度时,飞溅物 将从前部、后部以及各个方向上的毛细管侧壁喷出,尤其 在焊接方向上会有增加(见图 4)。总之,这些飞溅物很小,不会粘到工件表面。但是有一些大的飞溅物会污染到工件表面。尽管如此,其焊缝质量仍然非常好,焊接强度很大。
一方面,这种飞溅源于熔池振荡:流出的高能量金属 蒸气羽辉,沿激光光束向各个方向倾斜(见图 5)。另一方面,由于金属羽辉和入射激光束之间强烈的相互作用,这导致耦合的激光将在不同时段不同位置射入焊接工件。在光束方向上的发光效果使这种相互作用变得可见(见图4)。
图5:在3 m/min的进给速度下,不同时段的侧面图。
随着进给速度的增加,毛细管前 部变得越来越平坦。当进给速度增加 至 6 m/min,焊缝熔池表现出很高的动态性。结果显示,在毛细管孔径背 后的焊缝熔池开始膨胀,变得更加动 荡不安。一个有点不均匀的上珠出现。在这个焊接给进速度下,形成了一个 介于高速和低速焊接的过渡区。
当焊接进给速度进一步增至 8 m/min时,位于毛细管的尾部,在焊接进给速度(没有任何辅助切割气体)。这种效应被称为蒸汽压力熔切(VPMC)。图 2b 中分别显示了工件顶部、底部以及截面的焊缝质量。若将焊缝质量的等级以数字区分,1代表质量非常好,而6代表质量很差。我们可以看到,对于 12mm 厚的低碳钢来说,在激光功率为 8.7~10 kW 之间时, 可以实现深熔焊并获得良好的焊接效果。在实际工业应 用中,我们建议的选择功率为 9.25 kW(即大约处于功率 中点),以便增加激光加工过程的可靠性。正如上文提及, 该试验是在进给速度为 1m/min 的情况下进行的。
当焊接进给速度进一步增至 8 m/min时,位于毛细管的尾部,在焊接进给速度的反方向,将出现大量由熔化产生的飞溅物(见图4)。这不仅污染焊缝 表面,还将导致焊缝内大量材料损失,因而焊接无法得以强化,焊缝强度降 低,尤其在动态加载时。这种现象称 之为匙孔倾斜,在这种情况下激光功 率的吸收,更多发生在毛细管前部。随后熔化会使得材料吸收更多热量,并产生更大的蒸发率,这是激光焊接 中所有动态效应的推动力量。
如上所述,金属羽辉对飞溅和焊 缝质量也有很大的影响,因此同轴喷 嘴由此设计而成(见图 6)。压缩空气 在被吹向工件冷却熔池的过程中,同 时将金属羽辉吹离工作区域,从而降低激光光束与金属羽辉之间的相互影响。当焊接进给速度小于 8 m/min 时, 效果清晰可见(见图7)。
图6:同轴喷嘴与 cross jetz相连。
图7:在不同的进给速率下,使用和不使用同轴喷嘴情况下的侧面图。
由于在时间上和空间上,激光功 率可以被更加均匀地耦合到工件上, 毛细管内的蒸发也会更加均匀。从而毛细管变得更加稳定,飞溅带来的材 料损失减少。当焊接给进速度为 v < 6 m/min 时,相较于没有同轴喷嘴的 焊接,通常可以获得更高质量的焊缝 表面(见图8)。除此之外,使用同轴 喷嘴使得焊缝宽度变窄,并且增加了 穿透深度(见图 9)和穿透深度的稳 定性。
图8:不使用同轴喷嘴(a)和使用同轴喷嘴(b)时,顶部的焊缝质量。
图9:使用和不使用同轴喷嘴情况下的穿透深度和焊缝跨度。
转载请注明出处。