新能源汽车的持续火热,也为动力电池企业带来了新机遇。新能源汽车电池、电机、电控三大核心零部件中,动力电池在整车成本中所占比例最高,也直接决定整车性能。生产设备的精度和自动化水平将直接影响到电池的质量、效率和一致性。激光技术作为一种先进的加工技术,是高性能动力电池生产的最佳选择。
动力电池电芯根据外形可分为方形、圆柱、软包电池。方形电池电芯需要焊接的 部位有防爆阀、封口焊、注液孔焊接等,圆柱电池电芯需要焊接的部位有盖帽极耳、注液孔、封口焊等。除了电芯之外,电池成组PACK焊接也是需要激光焊接的,圆柱电池PACK焊接、方形电池PACK焊接、软包电池PACK焊接等。
不同的材料焊接工艺不同
壳体的材料主要有不锈钢和铝材,但铝材居多。不同的材料所采用的激光焊接工艺也不同,一般来讲,铝材的激光焊接功率难度更大,会面临焊痕表面凸起问题、炸火问题、气孔问题、内部气泡问题等。
不同焊接部位激光焊接工艺不同
以壳体的封装为例,根据位置的不同分为顶盖、底盖和侧面的焊接、顶盖防爆片及安全盖的焊接、注液口的焊接等。激光焊接方式可分为侧焊和顶焊,侧焊的好处在于电芯内部的影响较小,飞溅物不会轻易进入壳盖内侧,缺点是可能会导致凸起,对后续工艺有影响。顶焊的焊接是在一个平面上,对前道工序入壳和定位要求很高。
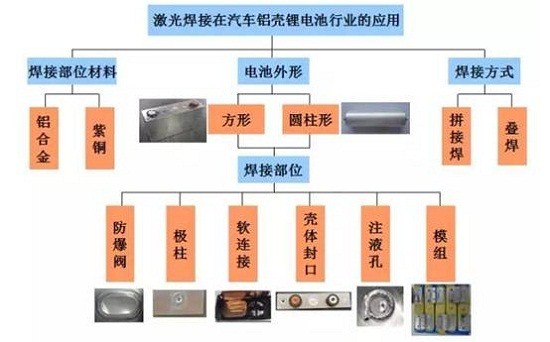
动力电池的激光焊接部位多,有耐压和漏液测试要求,材料多数为铝材及不同材料间的焊接,因此难度大,对焊接工艺的要求也更高。
华工激光将激光焊接技术与自动化,智能系统结合起来,打造了汽车动力电池全自动封口线,通过读条码识别产品种类,依次完成自动抽取真空、激光清洗焊接区域、自动上封并点焊和连续焊接及焊后检测。高精度完成上料、焊接流程,提高焊接质量和效率。
转载请注明出处。