High Speed Laser Cladding about to substitute hard chrome- and electroplating
based on the potential thread of lacking the allowance to use hard chrome plating for metal parts as of September 2017 in the EU, there is the need to develop alternatives. Thermal spray, already tested for this, offers a high flexibility but the quality of the achieved results is often not good enough. A very good alternative to hard chrome plating is the latest development of the extreme high speed laser cladding which was developed by the Fraunhofer ILT (Aachen, Germany) using equipment manufactured by Laserline GmbH (Muelheim-Kaerlich, Germany).
In power plants or other industrial manufacturing sites, metal parts are often under heavy duty in terms of wear and tear. The process parameters as well as the general production surrounding are often rough and lead to corrosion and abrasion to name the most important ones. To work against this and to allow a longer life of especially high priced parts in the production; these are coated with special layers. The entire surface of rotating parts, tubes and other functional components is covered with metal or ceramic layers.
This is increasing the resistance of the parts against heat, humidity, aggressive chemical substances as well as metal debris and spatter. An often and commonly used process is earlier named hard chrome plating. It is a galvanic coating method, whereas the part is dipped into a chromium electrolyte and thus, covered by a chrome layer. If there is the need of not coating special sections, those are covered up before dipping the component into the electrolyte bath. It is used especially as wide areas and big parts next to selected areas are possible to coat.
New coating technologies are necessary as chrome will be possibly banned
The future of hard chrome plating is hard to determine, even being very successful at this stage, because the commonly used Chrom-trioxyde, as well known as hexavalent Chrome, is marked as cankering and was marked in 2013 by the EU commission, in conjunction with other Chrome bindings listed in the annex XIV of the REACH regulation (Registration, evaluation, Authorization of Chemicals).This often discussed commandment regulates the usage of chemicals and lists in the mentioned annex the SVHC substances (Substances of Very High Concern). Those substances can only be used under a special and always timely limited certification from the ECHA after September 2017. Receiving this certificate is a highly complex procedure and even has several tricky issues in its process. For example it must be proven and guaranteed that any SVHC can be and will be handled absolutely safe in terms of the intended use and there are no alternatives to that explicit SVHC. For the well-established hard chrome plating it can be questioned if this is the case, especially if CrO3 is used. Thanks to this the iudustry using hard chrom plating is on a high alert and already lost a corresponding law suit with the European Court to further allow the use of Chrome in general.
based on these facts, there is no option for looking into alternatives as well as establishing those for any enterprise using the said technology. Anybody relying on chrome in general might risk is entire business model. Problem for all everybody is the limited amount of alternatives, which are available in terms of technology and being economic. Used in industry is thermal spay, in which the additive material is applied as powder. The powder is melted by a burner and “fired” against the surface of the to be coated part by a hot gas jet. The molten material is attached to the surface by mechanical bonding. The big advantage of this is the high flexibility of this process, as the coating can be done with a wide variety of different materials. The major disadvantage is the limited maximum mechanical stress-level. This is due to the mechanical bonding between the base material and the coated material, a bonding much less “belastbar” than those created by a galvanic process. Hence, coatings created by thermal spray are lost much faster. In addition the process created a porous surface and material layer, this easily leads to cracking and the latter often cannot be repaired by the initial process. Following this the result often is a partially transmissive layer which is not comparable to hard chrome plated coatings. To get around the porosity in the range of 1-2% the thickness of coated layers is increased which has an impact on the cost of the process. It is believed that thermal spray will maximum partially substitute electro plating.
Alternative is ultra-high speed laser cladding
A much better prognosis for the future is given to the powder based cladding process where a laser is the heat source. This Laser cladding uses the coated material as said as a powder, typically a metal powder. The laser radiation is melting both the metal powder as well as the base material and creates a metallurgical bonding as the two molten materials are joined together in a dilution zone. These metallurgical bonded layers are lasting much longer than comparable thermal spay created coatings and can even enhance the known wear resistance of galvanic coated parts. Furthermore Laser cladding results in a dense layer, free of pores and cracks and offers several advantages. However, the success in industrial applications was limited base on two major reasons. Firstly the layer thickness was limited to 0.5 mm or thicker and by this was excluded in some applications where a much thinner layer is required (Oil&Gas, agricultural and power plant applications). Second the cm² per minute was limited to 10 to 50 cm²/min which was the limitation for parts exceeding sized measured in meter rather than centimeter due to the speed.
For rotating applications this disadvantage got eliminated meanwhile by the Fraunhofer Institut für Lasertechnik (ILT).
In a lot of basic trials which were conducted on a specifically upgraded lathe using a Laserline LDF 4000-8, a diode laser with beam converter, it was shown that corrosion protective layers from a Nickel-Chrome alloy Inconel 625 were to be applied extremely fast with a speed of up to 200 meters / minute. This helped to reduce the layer thickness to 20 µm and in parallel increase the coated area to 500 cm²/min. All in all, the patented process of ultra-high speed laser cladding can achieve thicknesses between 10 and 250 µm.
The key to success was the increase of the intensity in the focal plane. Whereas standard laser cladding uses a spot size of 2-3 mm or even bigger, the new approach is based on a 1 mm spot size. Furthermore it was necessary to work on the positioning of laser spot, powder supply and shielding gases.
Whereas conventional laser cladding is melting the base material and the powder subsequently in this created molten pool - they only meet in this plane - ultra high speed laser cladding is heating the powder particles to a level which is close to the melting temperature and by this enhances the speed and helps reducing the layer thickness. The two process principles are shown in picture 1. The high temperature of the powder particles creates more or less molten particles which only require a short contact with the molten pool of the base material to create the desired metallurgical bonding. This leads to the increase of speed as compared to melting the particles in the melt pool in the conventional technology. In conjunction the energy required for the melt pool in the base material is much less. To apply the same amount of powder in some cases the necessary laser power can reach 20 kW whereas the high speed process only requires 2 to 4 kW of laser power. Thus, the process is more economic based on this efficiency and helps reducing the capital investment costs and higher running cost, too. Finally the result of this cladding process is a non-porous coating with a very low surface roughness, which only requires a limited amount of treatment after the coating.
With this new high speed process there is a new option available which outperforms the thermal spray technology in multiple points and with this is the most possible alternative to hard chrome plating.
Already in early 2016 the first customer project was realized based on this ILT developed and patented technology, using lasers from Laserline GmbH.
As the global interest is very high, the partners are working on many more projects and there will be a lot more installations in the industry soon.
As the process was initially only developed for parts which can be coated while rotating, there is now ideas and approaches to establish more options as well for coating of parts in a different shape.
Laserline and ILT will engage in more development consequently and apply the ultra-high speed laser cladding to more applications and purposes.
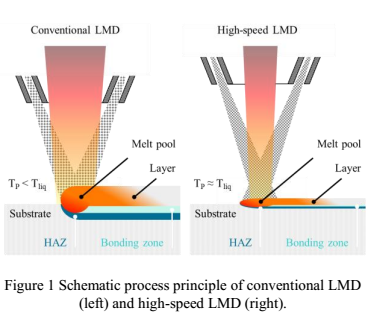
Source: Fraunhofer ILT, Aachen, Germany
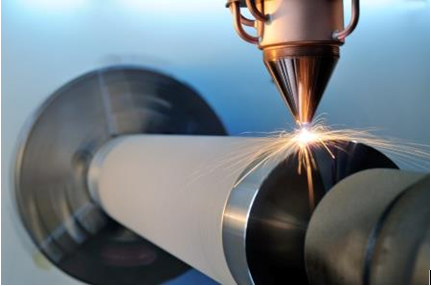
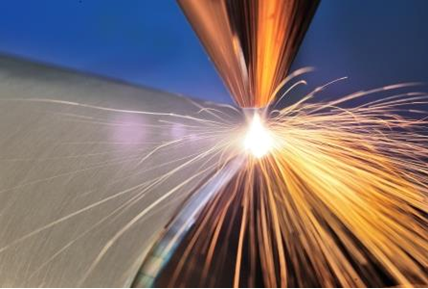
Picture 2 and 3: coating of a hydraulic plunger with ultra-high speed laser cladding
(source: Fraunhofer ILT, Aachen/Germany)
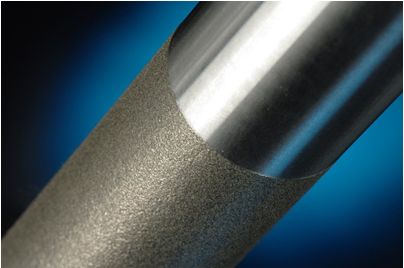
Picture 4: hydraulic plunger coated by ultra-high speed laser cladding and reworked by laser.
(Source: Fraunhofer ILT, Aachen/Germany)