LMD技术作为快速成型制造技术的一种,是通过快速成型(RapidPrototyping,RP)技术和激光熔覆技术有机结合,以金属粉末为加工原料,采用高能密度激光束将喷洒在金属基板上的粉末逐层熔覆堆积,从而形成金属零件的制造技术。整个LMD系统包括激光器、激光制冷机组、激光光路系统、激光加工机床、激光熔化沉积腔、送粉系统及工艺监控系统等。
LMD技术国外发展现状
增材制造技术发展经历了3个阶段,1892~1988年的技术孕育期、1988年开始的快速原型技术及20世纪90年代初期以来的直接增材制造。1979年,UTRC提出激光立体成形技术概念并制作出航空发动机涡轮盘模拟件;1994年起,Rolls-Royce探索航空发动机零件激光成形,另外英国利物浦大学和美国密西根大学、加拿大国家研究委员会集成制造技术研究所、瑞士洛桑理工学院、美国Sandia国家实验室、美国Los-Alamos国家实验室、美国Aeromet公司、美国宾州大学、英国伯明翰大学等都相继开展研究。由于LMD同轴送粉效率高,材料致密性好,因此,越来越多的用于大型零件的增材制造及零件修复工作。
国外有关大型零件增材制造技术的研究主要集中在美国。1995~2005年间,在美国国防部先进研究计划署及海军研究办公室等部门的巨额资助下,美国约翰哈普金斯大学、宾夕法尼亚州立大学及MTS公司等对飞机钛合金结构件激光快速成形技术进行了大量研究并取得重大进展,在此基础上,1998年由MTS公司独资成立了专门从事飞机钛合金结构件激光快速成形制造技术研发和工程化应用的AeroMet公司,与波音、洛克希德·马丁及诺斯罗普·格鲁曼等美国三大军用飞机制造商合作,在美国空军“锻造计划”(AirForce’sForgingInitiative)、陆军制造技术计划(Army’sMantechProgram)、国防部“军民两用科技计划”(DualUseScienceandTechnologyProgram)等资助下,致力于飞机钛合金结构件激光快速成形技术研究及其在飞机上的应用关键技术研究。2000年9月在波音和洛克希德·马丁公司完成了对激光直接成形钛合金全尺寸飞机机翼次承力结构件研究,构件静强度及疲劳强度达到飞机设计要求;2001年为波音公司F/A-18E/F舰载联合歼击/攻击机验证机小批量试制了发动机舱推力拉梁、机翼转动折叠接头、翼梁、带筋壁板等飞机钛合金次承力结构件,其中F/A-l8E/F翼根吊环满足疲劳寿命谱4倍要求,随后静力加载到225%也不破坏;2002年实现激光快速成形钛合金次承力结构件在F/A-18验证机上的装机应用。此外,美国还将应用于F-22接头的制造,试验结果表明其疲劳寿命高出寿命谱的两倍。
在LMD技术取得一定突破的时候,国外还将该技术广泛用于损伤零件的修复,包括飞机零部件腐蚀零件、航空发动机磨损等零件的修复。美国AeroMet公司采用激光成形技术完成了F15战斗机中机翼梁的检修;美国Optomec Design公司,采用激光成形技术进行了T700美国海军飞机发动机零件的磨损修复;瑞士洛桑理工学院采用激光成形技术修复单晶涡轮叶片。
LMD技术国内发展现状
我国在金属材料增材制造领域研究起步较早,技术研究及应用方面具有良好的基础,特别是在国家自然科学基金“重点项目”、国家“973”项目、国家“863”等重要研究计划重点支持下,增材制造技术得以快速发展。整个研究工作主要集中于北京航空航天大学、西北工业大学、北京有色金属研究总院、华中科技大学、清华大学等单位。其中在LMD技术领域上主要以北京航空航天大学、西北工业大学等少数几家单位。
在“十五”期间,北京航空航天大学突破了飞机钛合金次承力结构件激光快速成形工艺及应用关键技术,构件疲劳、断裂韧性等主要力学性能达到钛合金模锻件水平,2005年成功实现激光快速成形TA15钛合金飞机角盒、TC4钛合金飞机座椅支座及腹鳍接头等4种飞机钛合金次承力结构件(如图1所示)在3种飞机上的装机应用。
“十一五”期间,北京航空航天大学在飞机钛合金大型整体主承力结构件激光快速成形工艺研究、工程化成套装备研发与装机应用关键技术攻关等方面取得了突破性进展,提出了大型金属构件激光直接成形过程“内应力离散控制”新方法,初步突破大型金属构件激光快速成形过程零件翘曲变形与开裂“瓶颈难题”;突破激光快速成形钛合金大型结构件内部缺陷和内部质量控制及其无损检验关键技术,飞机构件综合力学性能达到或超过钛合金模锻件,例如,激光快速成形TA15钛合金缺口疲劳极限超过钛合金模锻件32~53%、高温持久寿命较模锻件提高4倍(500℃/480MPa持久寿命由锻件不足50h提高到激光成形件230h以上),特别是经后续特种热处理新工艺获得“特种双态组织”(图2所示)后,其综合力学性能进一步显著提高,疲劳力纹扩展速率降低一个数量级以上(图3)。
此外,激光快速成形出TA15、TC4、TC21、TC18、TC2等钛合金先进飞机大型整体主承力关键结构件、A-100等超高强度钢起落架等飞机关键构件、TC11、TC17、Ti60等钛合金整体叶盘等航空发动机关键部件并在飞机研制和生产中得到成功应用。
西北工业大学自1995年开始,在国内首先创造性地提出以获得极高力学性能为目标的金属增材成形技术构思,赋予“激光立体成形”之名,依托凝固技术国家重点实验室开展了系统的研究工作,建立起了包含材料、工艺和装备技术的完整的技术体系。经过近20余年的研究,针对大型钛合金构件的激光立体成形,解决了大型构件变形控制、几何尺寸控制、冶金质量控制、系统装备等方面的一系列难题,并试制成功C919大飞机翼肋TC4上、下缘条构件,该类零件尺寸达450mm×350mm×3000mm(图4),成形后长时间放置后的最大变形量小于1mm,静载力学性能的稳定性优于1%,疲劳性能也优于同类锻件的性能。此外,在LMD技术零件修复方面也取得了重大进展。TC4激光修复试样在低应变区的疲劳寿命高于锻件,在高应变区低于锻件,经过喷丸处理后及匹配修复后,高应变区疲劳寿命已非常接近锻件;图5所示为航空发动机轴承后机匣激光修复,通过激光修复轴孔径向缺陷,成形前安装边,恢复零件设计结构及尺寸,为该发动机首次装机试车提供合格零件;此外,还成功的应用于铝合金导向叶片、不锈钢机匣、钛合金压气机静子叶片、镍基合金高压一级涡轮叶片等修复。
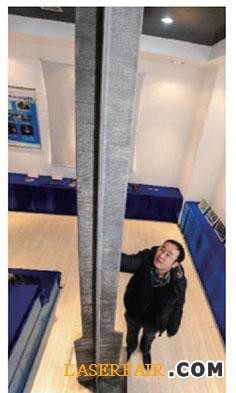
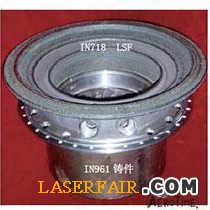