金属零件的激光增材制造技术(俗称3D打印)是从20世纪80年代发展起来的一项先进制造技术。增材制造的基本原理是根据零件的CAD模型进行切片分层处理,采用数控系统控制工作台按照分层软件设定的路径进行扫描,通过激光熔化金属粉末层层叠加获得近净成形零件。
增材制造技术的优点主要有:
(1) 增材制造技术可优化结构设计,拓展设计人员思路。受传统制造手段、加工方法的制约,很多优秀的设计理念难以实现。而增材制造技术不受产品零件形状的限制,解除这一限制后可以设计、制造出更轻、受力状态更合理的结构件。
(2) 零件精密成形,加工余量小,材料利用率高。采用传统制造路径时,大部分材料会被加工去除,成形零件不到毛坯重量的10%,造成了极大的浪费。而增材制造技术是一种近净成形技术,材料利用率可达90%以上,能有效降低材料成本,增强市场竞争力。
(3) 由于增材制造快速凝固的特点,成形件组织细密、性能优异。
(4) 零件生产流程短,工序简化,节省了大量加工时间,特别适用于小批量零件生产试制和产品零部件维修更换等需要快速响应的场合。
基于上述优点,自增材制造技术问世以来便引起了学术界和工业界的广泛关注,并在汽车、模具、航空航天业等领域获得了应用,并被认为是第三次工业革命和工业4.0时代来临的代表性革新技术。
金属零件增材制造技术根据粉末材料的送进方式可分为同轴送粉和粉末床两种。同轴送粉激光增材制造法又称直接金属激光烧结法(Direct metal Laser Sintering,DMLS),该方法成形效率高,能够制造大尺寸结构件,工艺开发时间早,技术比较成熟,但表面精度较差。粉末床工艺又称选择性激光熔化法(Selective Laser Melting,SLM),需先铺粉末再熔覆,成形效率较低,且受粉末床大小限制,成形件尺寸较小。但由于有粉末支撑,能成形异型复杂零件(如悬垂结构、镂空结构),成形件致密度和外形精度高。基于这些优点,近年来SLM技术逐渐引起了人们的关注。
本文对选区激光熔化增材制造(SLM)设备、粉末的研制情况、需解决的关键技术问题进行了梳理,并对该技术在民用飞机上的应用前景进行了展望。
SLM设备研究情况
在国外,SLM设备研究主要集中在德国、法国、英国、日本、比利时等国家。德国对SLM技术及设备研究早,技术也比较成熟。第一台SLM设备由德国MCP公司推出。目前德国EOS公司是全球最大,同时也是技术最领先的激光粉末熔化增材制造成形系统的制造商,目前设备主要有EOSINT M280(图1)和EOSINT M400两款。EOSINT M280激光烧结系统采用的是Yb-fibre激光发射器,高效能、长寿命,光学系统精准度高。M280能成形的零件最大尺寸为250mm×250mm×325mm。而最新推出的EOSINT M400设备选用的激光器功率更高,能成形的结构件尺寸更大,最大尺寸达到400mm×400mm× 400mm。德国的EOS公司在国内销售业绩良好,国内多家单位采购了EOS公司的SLM设备。
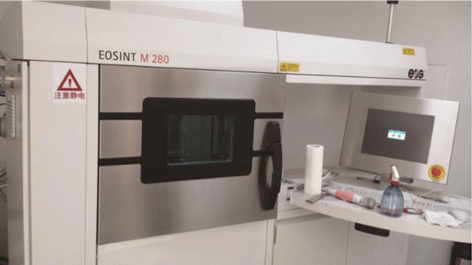
图1 EOS公司INT M280设备
在国内,开展SLM设备研制的单位主要有华南理工大学、华中科技大学,武汉光电国家实验室等[1-5]。其中,华南理工大学在2006年就联合几家单位开发了一套SLM快速成形设备,2014年又在前期的基础上加以改进,生产出Di-metal 100型设备,主要参数为:SPI连续式200W光纤激光器(波长1075nm),光斑直径50~70μm,最大成形尺寸100mm×100mm×100mm,铺粉层厚20~50μm,扫描速度5~7000mm/s, 成型腔室以Ar或N2保护,含氧量控制在0.1%以下[1-2]。华中科技大学研发的HRPM-Ⅱ型设备主要参数为:100W连续模式光纤激光器,采用二维振镜聚焦,激光定位精度0.02mm,最大扫描速度5m/s,成形速度≥7000mm3/h,铺粉层厚50~100μm,采用双缸上送粉方式,最大成形尺寸为250mm×250mm×400mm。该设备在超轻结构复杂件的制备方面有较强的优势[3]。此外,武汉光电国家实验室也自主研发了SLM设备,并对该设备的铺粉装置、运动控制系统、总体集成技术等进行了深入研究[4-5],其设备能实现与德国EOS公司设备相对应的功能,且在价格方面具有优势,已经在航天企业中获得了应用。
SLM专用金属粉末研发情况
SLM技术与粉末冶金技术(Powder metallurgy,PM)是互相联系而又有所区别的两种技术,共同点在于二者都是从粉末原材料通过加热致密化制造出相应结构件,区别主要有两点:(1)粉末冶金过程中,加热的同时还要加压,粉末未完全熔化,而SLM主要通过激光完全熔化粉末进行制造;(2)采用粉末冶金的方法,粉末是一次性放入的,而SLM中的粉末是分多批次逐步加入的。这些区别导致二者对所用的粉末原材料要求有很大不同。
粉末冶金技术发展的历史较为悠久,国内相关行业标准较为完善,配套粉末生产企业也比较齐全[6-7]。然而,目前生产SLM专用金属粉末的主要是国外企业。其中,德国EOS公司规定成形所用的粉末材料也必须使用公司的配套产品,否则零件的成形效果就达不到质量要求。而EOS公司的粉末定价高,从国外进口采购周期长且面临限购、运输安全等风险。因此,立足国内研究情况,自主生产SLM专用粉末是必要的。在SLM专用粉末的生产方面,国内比较知名的有无锡飞而康快速制造有限公司、西安铂力特激光成形技术有限公司、西安赛隆金属材料有限公司、沈阳金属所等。主要是利用感应熔炼气体雾化技术生产粉末,并通过筛分获得不同粒径大小的产品。整个生产过程需在惰性气体保护下进行,避免外来杂质污染。
SLM技术在民用飞机上的应用前景
随着技术进步及人民生活水平的提高,公众对民用飞机的经济性、环保的要求越来越高,这对民用飞机的制造技术提出了更高的要求。减轻飞机结构件的重量能有效降低材料成本和燃油消耗,提升飞机的市场竞争能力。增材制造技术由于能有效改进结构设计,减少材料用量,缩短加工流程而倍受关注。包括波音、空客等大型民用飞机制造商都投入了大量的资金、人力、物力对这一技术进行研究,并已取得了显著成果,在飞机发动机、吊挂、襟翼、舱门等部位已有成功的应用。例如:空客公司在A300/A310机上厨房、盥洗室和走廊等连接铰链上应用了增材制造结构件,并在其最新的A350WB型飞机上应用了Ti-6Al-4V增材制造结构件(如图2所示),且已通过EASA及FAA的适航认证。GE公司采用增材制造技术制造了Leap喷气发动机的金属燃料喷嘴,通过这一技术,将喷嘴原本20个不同的零部件变成了1个。这样造出的燃油喷嘴重量更轻,而且能够承受极端温度,为该公司节约了大量成本。近期GE拟采用增材制造技术制造GE9X喷气发动机的低压涡轮,GE9X据称是“有史以来建造的最先进、最省油的商用飞机发动机”,这款发动机将成为波音777客机的下一代——777X客机的驱动引擎,该款机型将于2017年开始生产,并有望在2020年交付首架给客户。
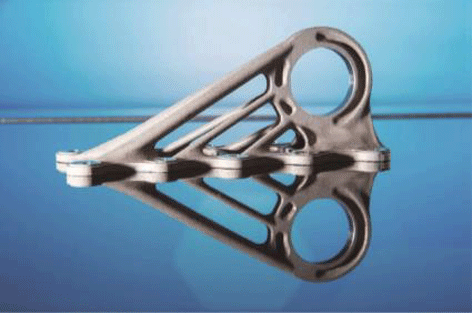
图2 空客公司采用SLM技术制造的Ti-6Al-4V结构件
国内在SLM技术的研究上也取得了一定的进展,不过相比之下,其技术的发展还不够成熟,要实现在民用飞机上的应用,仍有大量的工作要做,例如解决SLM成形本身的技术问题,研究成形件后续处理工艺技术,并编制相关标准规范制度,进行结构件的适航认证等。图3所示为国内企业用SLM技术成形的复杂零件。
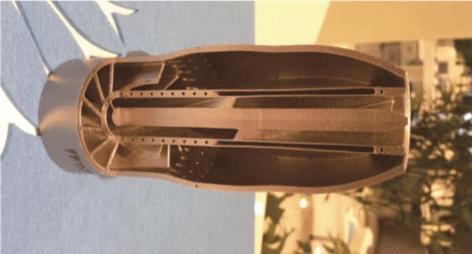
图3 国内企业用SLM技术成形的复杂零件
目前,SLM技术的关键工艺技术有两个:成形过程中粉末的球化现象和制件存在孔隙、裂纹等缺陷问题。球化现象是指在激光成形过程中,金属熔化后形成大量彼此隔离的金属球,破坏成形金属表面质量,严重时阻碍铺粉辊的运动,使成形过程无法继续进行下去。孔隙的形成则使得成形件致密度低,严重影响其性能。在SLM成形工艺方面,南京航空航天大学的顾冬冬教授做了很多工作[8-10],分析了铜基合金、不锈钢等材料成形时的球化分析机理,提出可通过预热粉末床,控制激光扫描速度和线能量密度等方式减少球化;此外还研究了铜基合金的孔隙率与加工参数的关系,并指出合理控制能量密度是减少孔隙产生,提高制件性能的关键。
由于用SLM技术制造出来的零件表面质量和尺寸精度不能满足最终使用状态要求,因此还需对增材制造结构件进行少量的后处理,如机械加工、热处理、表面处理等。这就要求对SLM制件的后处理技术进行研究,将其与传统的锻件、铸件的加工性能进行对比,找出合理的工艺参数。
此外,民用飞机还有一个很大的特点,就是所有的材料和制造方法必须经过适航认证才能实现装机应用,这就要求制定相应的材料规范和工艺规范,并向负责适航审定的局方演示,获得局方的认可,这方面也是国外走在前列[11]。例如: 2013年美国汽车工程师协会(SAE)制定了Ti-6Al-4V粉末的航空材料标准AMS4998E。2002年SAE制定了直接沉积Ti-6Al-4V产品航空材料标准AMS4999,2011年将其升版为AMS4999A。此外,美国材料测试协会(ASTM)已发布两项有关粉末床熔覆钛合金的标准,分别为ASTM F2924-14:粉末熔覆床工艺增材制造Ti-6Al-4V标准规范和ASTM F3001-14:粉末熔覆床工艺增材制造Ti-6Al-4V ELI标准规范,这些规范规定了用于增材制造的粉末、设备及工艺方面的要求。而国内关于SLM标准规范方面的工作却仍十分欠缺,国内航空工业界仍需付出艰辛的努力。
结束语
本文简要介绍了选区激光熔化增材制造(SLM)技术的特点和发展现状,总结了国内外关于SLM所用的设备、粉末原材料面临的关键技术难题等情况,分析了这项技术在民用飞机上的应用前景,对促进SLM技术在民用飞机上的应用有一定的参考意义。